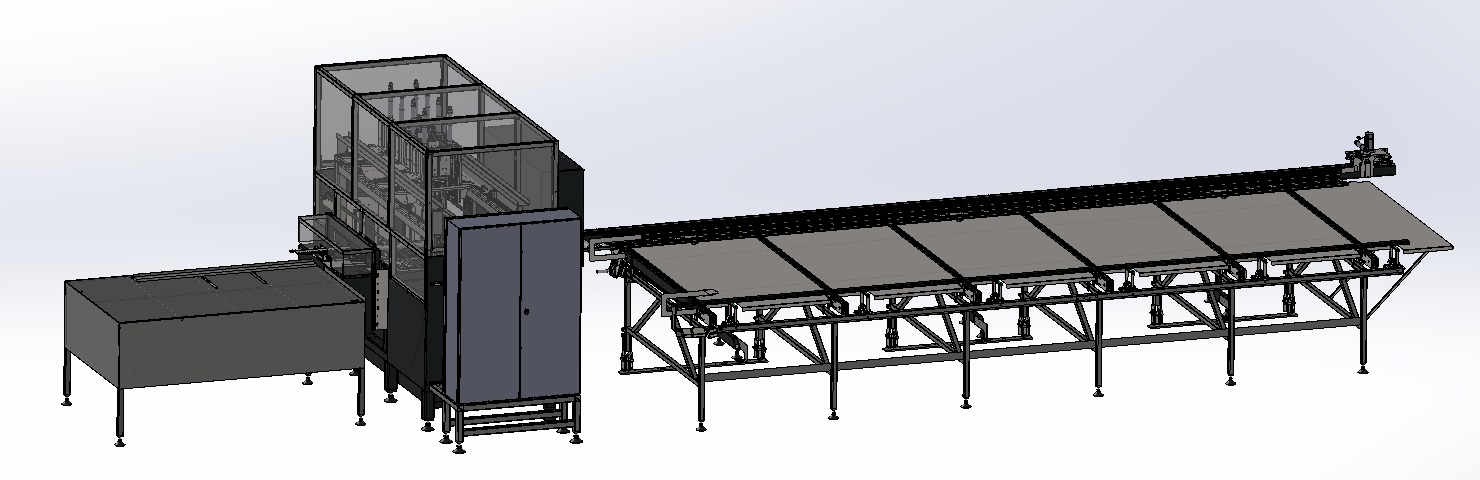
This version of the production line allows fully automatic processing of plastic profile bars made of (PVC, PE, PP, PC, PA, SI, PVAC, PTFE,) up to 6,500 mm in length. The line is composed of interconnected segments – modules, the work coordination of which, as well as the simultaneously running production processes in them, is controlled by a custom-written CNC line control program AZIMUT.
LINE MODULES AND SEGMENTS:
- "Dynamic" CNC single-axis motorized belt conveyor with intelligent gap-free documenting function, including loading bridge, and pneumatic sliding and straightening mechanism. Integrated between the belt supports, for soft plastics and integrated adhesive layer on the conveyor belts for slippery materials. Designed for profiles included in the specification up to L=6,200mm
- "Huricane" CNC single-axis motorized positioning feeder with magnetic tape measurement and push, position, pull functions.
- "Kreator" CNC six-axis input machining unit for longitudinal edge trimming and bottom milling, grooves. 3 x working electro-spindle, each separate, CNC two-axis motorically interpolated to position.
- "AZIMUT" Main CNC machining unit equipped with three-axis helical interpolation of one or two tools working simultaneously. CNC single-axis motorized pitch positioner, for two tools working simultaneously. 8 x working electro-spindles, each equipped with separate pneumatic shifting of working and basic positions.
- "Trajektoria" CNC two-axis motor system for positioning the sawing unit during the work cycle. 1x flat saw motor. Controlled trajectory of the cutting unit allows copying of various surfaces, ensuring controlled removal of sawdust, optimization of cutting time, progressive extension of tool life as well as minimizing energy consumption per cut. Return of the saw to the basic position under the work table shortens the time for feeding the material to a new position and at the same time ensures a cut without back abrasion. (Due to productivity, clean cut and controlled direction of sawdust, our new approach to cutting thus relegates to the past, previously common and progressive cutting methods, which were considered, for example, controlled opening of the cutting gap when the cutting blade returns.)
- "Ejector" Automatic ejection mechanism for finished pieces
- "Retro" Transport and assembly table for finished pieces, specially designed table extension for oversized pieces, as well as for shaping and milling longitudinal grooves on the entire bar.
BASIC CHARACTERISTICS OF THE LINE:
- HMI touch panel as a dialogue window for the machine operator. It has a complete menu for:
- selection of machining programs
- collection of statistical data
- three-level service menu
- factory settings
- The AZIMUT module is equipped with a CHECK TOOL sensor for automatic calculation of corrections in programs for a newly installed tool
- CNC motor positioning of the processing units is via ball-nut screws SFU2510; SFU1605 and SFU1610, along linear guides fitted with HGR20 carriages
- Equipped with DELTA electronics / HMI, PLC, SERVODRIVERS, SERVOMOTORS, INVERTERS /
- HERTZ frequency-controlled electro-spindles
- Machining accuracy ±0.1mm
- Fully automatic operation after loading the magazine.
- Beacon signaling of device status
- The machine is equipped with an internet connection and EWON device for remote management