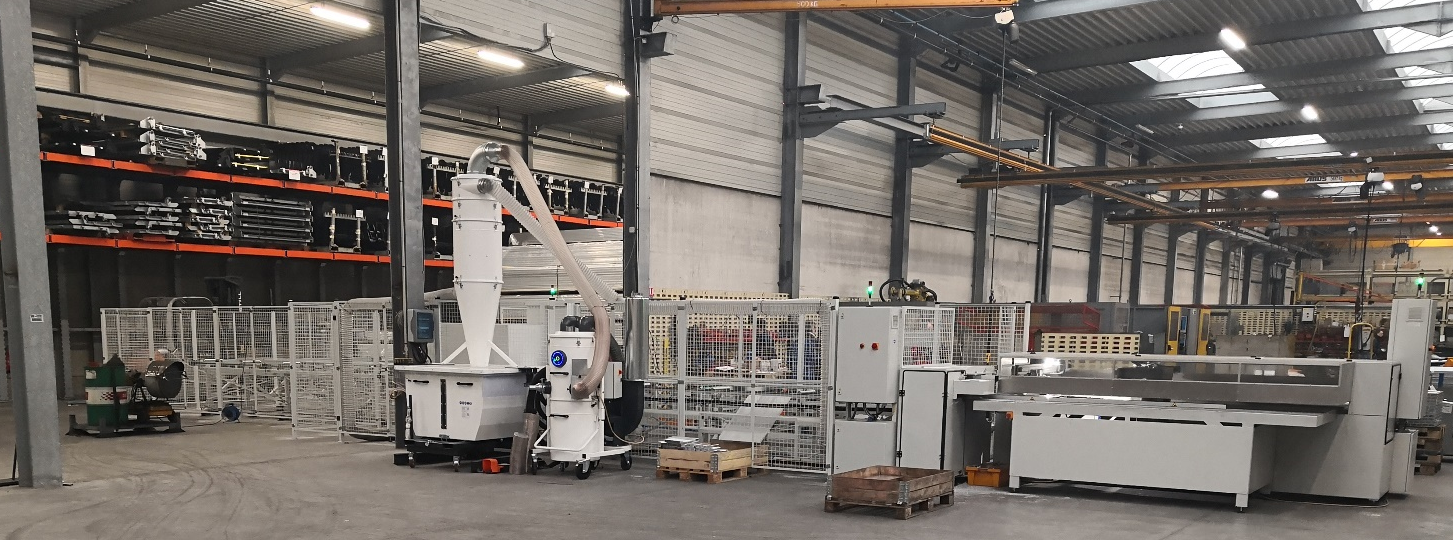
DYNAMIC line models:
DYNAMIC 0 / for profiles L=3 000 -7200; W=100-360; H=20-35 -51 /mm
DYNAMIC 1 / for profiles L=3 000 -7200; W=100-360; H=20- 35 -51 /mm
DYNAMIC 2 / for profiles L=6 000 -12 500; W=100-360; H= 20-35 -51 /mm
DYNAMIC 2H /for profiles L=6 000 -12 500; W=100-360; H= 20-35 -51 /mm
The DYNAMIC line is designed for complete processing of profiles intended for the production of hydraulically operated handling platforms for commercial vehicles and trucks. The subject of automatic processing are hollow aluminum profiles from 100mm to 360mm wide, from 20mm to 51mm thick, and from 3,000mm to 12,500mm long.
The line is composed of three interconnected machine nodes:
Sector 1/ is designed for continuous multi-directional milling of anti-slip grooves. It has a device for semi-automatic loading of profiles onto an intelligent transport magazine, a milling machine for continuous milling of anti-slip patterns and an inter-operational magazine of profiles for automatic transfer of the grooved bar to node two.
Sector 2/ is designed for cutting notched bars to lengths given by the program. The node is equipped with a servo-motor vice feeder. The feeder position is detected from a magnetic tape with a value of 4p/0.01mm. The saw control has a servo-motor drive of the cutting unit with automatic cross-section height adjustment, frequency-controlled speed, a cutting gap expansion function, an overflow hole for cuttings, and an integrated discharge device for cut pieces.
Sector 3/ is designed for simultaneous double-sided end milling of base grooves. It is equipped with a receiving table for cut pieces with a moving and centering device. The milling machine has fully automatic servo-motorized vice jaws that move the profile between the milling assemblies and transfer the finished machined piece to the removal table. The receiving table is also equipped with a BYPASS function for profiles without grooving.
The line is equipped with:
Touch panel, for each node . The panel is used to control and start production processes, like a dialog box for the machine operator. Each panel displays the current progress of the machining program in the cycle.
Software-controlled cutting tool lubrication system , in all machining locations. The software monitors the cutting fluid level. It also controls the precise dosing and method of spraying the cutting micro-mist, through dual solenoid injectors with media transport, hose in hose (2.5mm/6mm) terminated with a precisely oriented chip.
Software for automatically collecting statistical data for customer needs
about the quantity of pieces produced of each type and length / shift, week, month, year /
about engine hours and average cycle times
about compliance with prescribed maintenance cycles ....
EWON remote access and management system in the form of
troubleshooting, checking the functionality of individual components
diagnostic performance
editing, proofreading and software management
The sawdust extraction from individual nodes can be connected to central extraction systems. If these are absent, a powerful extraction device with a cyclone and a collection container with a volume of 1000L is connected.
Basic description of the line configuration set
The loading of the profile bar into the intelligent transport container is carried out using the MAGIO II or Magio III loading manipulator in cooperation with the line operator. The transport conveyor of the first node has a capacity for 10 profile bars. It has a function of intelligent bar documentation, so that there are no empty spaces on the conveyor.
The process of taking the profile bar into the "ROTATOR" grooving mill and setting the milling parameters for a specific profile is fully automatic. The profile type is identified using sensors, the milling unit and the transport device for continuous feed of the profile through the milling machine to the central conveyor of node II are automatically set.
The conveyor of node II has a capacity for three notched bars. Incoming, waiting and moved. The bar is fully automatically moved to the "PREMIUM" tong manipulator. The manipulator is equipped with a floating vice to eliminate the unevenness of the long bar when cutting it to the required lengths. The cut lengths are given by the program. The accuracy of bar positioning in the "AL CUT 90" saw is given by independent measurement from a magnetic tape. The achieved accuracy of the cut pieces is +/-0.1mm absolutely. Similarly, all movements in the saw are servo-motor, controlled by the program for each type of bar. The cutting unit is automatically positioned in the height of the blade extension, in the length of the cutting path, and the dynamics of the movement into the cut and also for the return. The program equipment also ensures the automatic expansion of the cutting gap when the blade returns. The alignment piece and the cutting residue automatically end up in the collection containers designated for this purpose. The feed device integrated in the saw automatically moves the cut piece to the positioning table of Node III of the "MERCURY" groove milling machine.
The receiving table of node III has a cutting BYPASS function. The feed mechanism automatically moves profiles that do not require further processing to the removal position. The removal surface is equipped with a filling sensor. Profiles intended for end milling of positioning grooves and grooves for the outflow of anodic oxidation liquid are automatically positioned for the vice jaws of the two-unit milling machine "MERCURY". Each unit has an automatic shifting of the corresponding assembly. The milling units are automatically positioned in the longitudinal and vertical direction so that both ends of the profile are processed at the same time. The profile is automatically clamped in the vice jaws, lifted and servo-motorically transferred through the milling assemblies to the output side of the milling machine. Here it is automatically placed on the output table and pushed out of the machine to the removal point. The table is also equipped with a filling sensor. Continuously perpendicular, the profile passage through the milling units with changing cutting resistance is ensured by software for controlling the synchronous electronic mirror transmission. The grooves are milled with an accuracy of +/- 0.1mm